The Drift Electric Vehicle Concept
Post on: 16 Март, 2015 No Comment
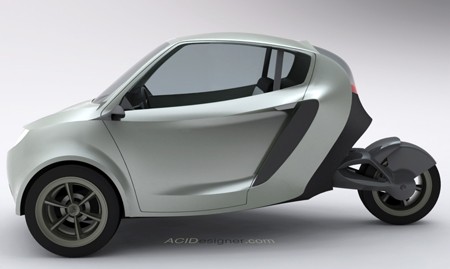
A two wheel front or rear or all wheel drive street or rally car featuring an off the shelf lightweight aluminium chassis, a carbon fibre reinforced plastic body tub, in-hub electric motors, dual carbon batteries and free piston linear generator range extenders. All of these technologies are at the edge of innovation in electrical vehicle development. Theodore and Associates have a simplified chassis design the Uni-Chassis to drop into a flexible vehicle configuration. Local Motors has manufactured a CFRP 3D printed car prototype. Protean Electric has a high performance in-hub drive motor that eliminates all conventional drive train components. In a rear wheel drive configuration the peak power output is 200hp (150kW) – double that for a four wheel drive configuration. Power Japan Plus has an improved battery with a more usable power range, lower costs, greater thermal stability (eliminating complex cooling systems) and which is completely recyclable. DLR has a new ultra flexible fuel range extender that completes a brand new electric vehicle concept with all the range and reliability you need (and more) in a high performance and flexible, low cost, low weight package. Introducing a Local Motors concept that I have taken the liberty to rebadge as the Drift EV.
The design uses plug and play components available or soon to be available in the case of DLR range extenders from global suppliers. The flexibility of the components allows for a number of drive configurations front, rear or all wheel drive different chassis lengths and widths and different body configurations.
The all wheel drive model with 22 inch wheels and classic styling aims for understated supercar performance at a modest additional weight and cost penalty.
The key to light weight vehicles is the use of composite materials and high strength bonding agents. The concept is illustrated in the Lotus Evora with multiple grades of aluminium bonded and riveted (allowing use of thinner sections) along with a molded resin composite body tub and a high strength steel rear crumple zone.
The combination of a rigid backbone structure connecting front and rear structures; in combination with the front and rear suspensions affixed to the to the front and rear structures; to create a complete, self-supporting chassis, without the need for a separate frame….
A plug in aluminium design with established front and rear crash dynamics. The Theodore and Associates Uni-Chassis is shown with a Shelby Cobra body.
Because of the heavy use of extrusions and the six castings, tooling costs also are lower than a typical spaceframe, according to Theodore: “Conservatively, we estimate 10% less, although one study indicates more. The real investment savings comes when you apply Uni-Chassis to a family of vehicles. Wheelbase can be increased basically by increasing the length of the backbone extrusion and quill shaft (of course, front and rear structures need to be designed to handle the platform bandwidth), spreading investment costs among multiple vehicles.”
Front, rear, and offset impact loads are handled in much the same manner as conventional structures, with crush beams attached to the front and rear of the Uni-Chassis. And because most of the vehicle mass is carried by the Uni-Chassis in front and rear impacts, body impact loads are minimized—much like body-on-frame construction.
“One potential advantage is that Uni-Chassis decouples chassis and body crashworthiness requirements, such that the decel pulse can be ‘tuned’ by both the Uni-Chassis and the interaction of the body to the Uni-Chassis,” Theodore explained. “On the other hand, the body structure must still be designed for side impact, rollover, and restraint system loads, much like a pickup cab.”
Finite-element modeling indicates that torsional stiffness is equal to or greater than competitive supercar chassis. Bending stiffness is claimed to be much higher.
“The combination of a rigid backbone structure connecting front and rear structures; in combination with the front and rear suspensions affixed to the to the front and rear structures; to create a complete, self-supporting chassis, without the need for a separate frame….
Other advantages include:
¤ Weight, cost and investment savings
¤ Battery Box on Plug-in Hybrid and BEVs doubles as the backbone
¤ Adapt different bodies to the same Uni-Chassis™
¤ Uni-Chassis™ is scaleable to different size vehicles by varying backbone length
¤ Uni-Chassis™ is modular, allowing different powertrains within the same architecture
¤ Creates a “rolling chassis” before installation of the body
¤ De-couple chassis loads from body loads
¤ Decouples chassis and body crashworthiness requirements
The key to cutting costs for mass market vehicles is Carbon Fiber Reinforced Plastic (CFRP) bonded with high tech glues and riveted to the aluminium chassis. CFRP lends itself to digital additive (3D printing) manufacture providing a low cost highly flexible approach to producing different configuration in body tubs in a local and low volume production environment. The prototype is the Local Motors Strati.
Each of these puts out 75kW peak power (54 continuous) – with four wheel drive that’s 400hp peak power. A 2wd configuration results in a lower cost – and is what drift cars are all about. Indicative pricing for these motors is US$1600.
‘Protean Electric has designed and developed a unique in-wheel electric drive system for hybrid, plug-in hybrid and battery electric light-duty vehicles. The Protean Drive™ system can improve vehicle fuel economy, add torque, increase power and enable improved vehicle handling to both new and existing vehicles. Protean Drive™is a fully-integrated, direct-drive solution that combines in-wheel motors with an integrated inverter, control electronics and software – no separate large, heavy and costly inverter is required. Each motor packages easily in the unused space behind a conventional 18- to 24-inch wheel and can use the original equipment wheel bearing. The direct-drive configuration reduces part count, complexity and cost, so there is no need to integrate traditional drivetrain components such as external gearing, transmissions, driveshafts, axles and differentials.’ This Brabus E-class Mercedes conversion shows what’s possible.
Battery cost, reliability, safety and the environment impacts of rare earths and heavy metals have been a constraint on EV development. The dual carbon battery fromPower Japan Plus promises to balance the energy storage equation . Superfast charging is a bonus.
‘For manufacturers the dual carbon battery offers a high-value, high- performance product with no switchover cost. For electric vehicle companies, production simplicity combined with great performance will unlock true mass-market electric vehicles. The dual carbon battery slots directly into existing manufacturing processes, requiring no change to existing manufacturing lines. Even more, the battery allows for consolidation of the supply chain, with only one active material — carbon. Additionally, manufacturing of the dual carbon battery is under no threat of supply disruption or price spikes from rare metals, rare earth metals or heavy metals. Even more, the thermal stability of the battery eliminates the need for complex battery cooling systems. The dual carbon battery also fits any form factor.’
Battery chemistry is evolving rapidly and use of available technology facilitates development and allow cell chemistry to be updated as battery technology evolves. Battery packs for current generation EV use Lithium ion chemistry and it is possible to slot in an advanced battery pack and management system from AC Propulsion designed for weight minimization and optimized for 150kW peak power and 100kW continuous.
Free Piston Linear Generator Range Extender
The range extender is a fossil fuelled on board battery charger. The Chevy Volt uses a 1.4L petrol engine for instance. The free piston linear generator is the next step. It does away with most of the moving parts of conventional internal combustion engines. In the simplest configuration it consists of magnets mounted on pistons and a coil surrounding the cylinder. DLR and Toyota are both testing versions. The DLR device is described by gizmag ‘The explosion of the fuel-air mix pushes the pistons on either side of the central combustion chamber towards the gas springs, which decelerate the pistons and push them back. The device operates at a frequency of 40 to 50 Hz and produces up to 35 kW of power.’
Three combustion chambers would be used to supply full continuous power to the drive wheels with a total weight of some 120kg.
Technology offers the potential for a low cost electric vehicle with a top speed of 200km/hr, a range of 600km and an ultra low center of gravity and individual wheel control for exceptional handling dynamics. The Drift EV concept brings global resources to a local manufacturing capability to produce simpler, cheaper and more robust performance orientated electric vehicles.
These are technologies at the prototype or test bed stage that offer opportunities to change the EV landscape – along with off the shelf components that have demonstrated capabilities.
While the technologies are innovative – the guiding principle is to build a flexible platform that may be adapted as the technology evolves.
A version of the opposed cylinder motor has been developed by Achates Power. It is some 20% more efficient than diesel engines and 55% more efficient than petrol.