The Gatekeepers Consultants Hold The Key_2
Post on: 16 Март, 2015 No Comment
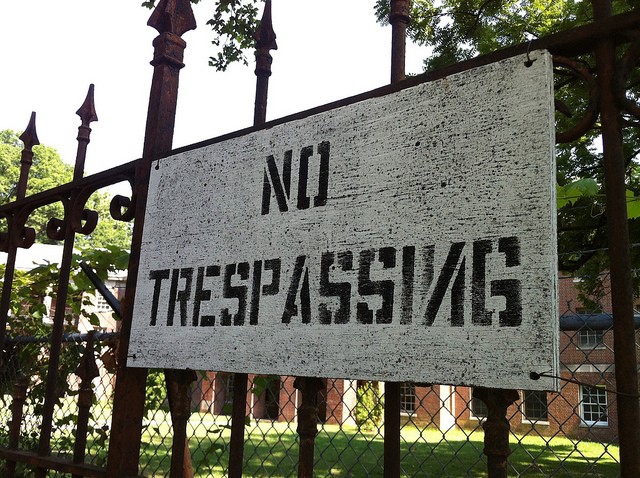
QC Inspections for Hand-Made vs. Machined Products
A reader asked me an interesting question:
Every article I read on your blog assumes machined manufacturing and I wondered how would quality control be different with handmade products where human factor play the most important role?
The short answer is: no I dont assume machined production, and yes quality control should take this information into account (but only when production is under way).
And here is my long answer.
The notion that “quality is uniform since the products are machine-made” is very dangerous.
Sometimes it is true. Here are a few examples:
- All the pieces go through one machine that is precise but biased (poorly calibrated). All the pieces come out too thin.
- The thread used for the bartack stitching operation is in the wrong color.
- A wood furniture manufacturer selects an out-of-date program for the automatic cutting machine. All the products follow an old design the importer doesnt want.
However, it is often wrong. Here are some counter-examples:
- Half the components are out of specifications but they are used in production anyway because incoming QC procedures are not appropriate and/or not effective.
- Four similar machines were used simultaneously to produce a batch. In one of them, a critical component is severely damaged (inducing much variation) but has not be noticed yet by the maintenance technicians. (Note that maintenance is very poorly done in most Chinese factories.)
- One of the process steps is to harden the products in a kiln. The kiln worked fine for 90% of the batch, but a power shortage means 10% of the batch was not processed correctly. The factory naturally assumes they can ship those goods anyway — after all they did go through the kiln and they did get a heat treatment.
- A testing station doesn’t detect a serious flaw in an electronic product.
- The factory ran out of components after making 95% of the batch because of unforeseen scrap. The quantity to replenish is too low, and the lead time to get it is too long. The factory decides to ship that scrap to its customer. This is unfortunately frequent in China.
Now, what are the implications?
1. From an end-of-production-quality-control perspective I would follow the same inspection procedure for all types of products. The inspector needs to do a proper sampling and takes pieces from different cartons, since 5% or 10% of the order might be defective.
The right approach for final random inspection is “make no assumptions”. Skipping some checkpoints or reducing the sample size is quite dangerous if the buyer is not fully aware of what can go wrong in production. From experience, I believe the ISO 2859 (AQL) standard is appropriate whatever the production process. It has the advantage of being simple and of being widely known by Chinese suppliers.
2. From a process control perspective there are differences.
2.1 For a highly automated process. the manufacturer needs to pay a lot of attention to these elements:
- Management of setup programs
- Preventive maintenance of automated equipment
- Calibration of gauges
- In certain industries, statistical process control
And in-process quality control should be regular along the production cycle. Not only at the very beginning.
2.2 For a manual production process. critical success factors are listed below:
- Training the staff and writing good work instructions
- Having operators fully understand that bad work should never be passed to the next station
- Coming up with good tool, dies, or fixtures to make it easier to do a good job
- Mistake proofing operations as much as possible
3. From a “it is not acceptable and you need to do re-work” perspective it is also different.
In most cases, a manual sorting is necessary after some issues were found. The importer asks the manufacturer to check every piece, to sort out the “bad” ones, and to re-work/reproduce/discard them. A Chinese factory that focuses on labor-intensive work will have a lot of people to throw at this job (but they might be unable to find the defects that caused the rejection), while the more automated supplier might be unwilling to do so.
Let’s assume the sorting was done properly. The second step is, in most cases, to rework the faulty pieces. If processes are manual it is often possible (but the question is, will do it right the second time if they messed up the first time?). In machining or fabrication workshops, it is often impossible — they might have to scrap those parts and re-produce them, which is often long and costly.
To recap, in a final inspection the buyer should not assume “this comes out of a machine so I can check one piece and all the others will be exactly similar”. But I strongly encourage buyers to pay attention to the factory’s process controls. We have found nearly every time that improving process controls results in better quality and lower costs.
What do you think?
Quality, Fact or Fiction?
This is a guest post by Jo Van Landeghem. Quality and Safety manager for global retailer C&A. Jo and I have exchanged emails a few times and I like his approach that I find refreshing and interesting.
What is Quality? Calidad, kachestvo, qualität, quales, qualité, Zhiliàng, kalite, Khunphaph, kvalitet, qualita, Hinshitsu An age-old question never fully agreed upon by all but nonetheless oh so relevant in the money ruled world that we live in.
In the manufacturing world, quality is quite straightforward. It is seen as the state of being free from defects, deficiencies and significant variations. Quality is created by strict and consistent commitment to certain standards that achieve uniformity of a product in order to satisfy specific customer or user requirements. There is even even a standard (ISO 8402-1986) that defines quality as the totality of features and characteristics of a product or service that bears its ability to satisfy stated or implied needs.
According to my grandmother, a product is of good quality when it performs exactly as per the customers expectations. The same applies to providing quality service to a customer. Quality is also the result of continuous effort to deliver beyond the customers expectations.
And according to my first High Street Fashion mentor, quality is the emotion of luxury and uniqueness it provides.
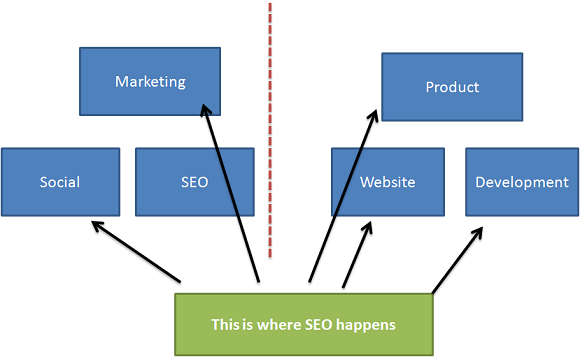
Actually all are correct. There is an aspect of Technical quality influenced by the workmanship, finishing, materials used, and so on. And there is also an aspect of Emotional quality involved which is influenced by the hand feel, styling, look or general emotion the brand name incurs.
When thinking rationally and taking into account the planets limited resources, Quality should also be equal to durable, timeless, easy maintenance, easy to use, 100% recyclable, functional, low carbon footprint, simplicity in design, reliable, friendly to the environment, healthy, and safe.
Can all of the above fit together in our current world? They can, if we are willing to commit to better quality! As it will influence the buying behavior of the customer, the selling price of a product, the profit margins, a reduction in discarded product, less pollution, a lower impact on the planets resources and on the way products are sold and used. Companies will have to transform, but those working on sustainability have already realised it is the only way forward.
Is there then a need for quality? Look around you. How many products are out there that are just a waste of money? Take for example very cheap electronics, DIY tools, clothes, furniture well almost anything that is ridiculously cheap. How often have you turned down a product about which your emotional side said at that price I just buy it and if it no longer functions Ill throw it away? Well very often you end up throwing it away. Millions of products like this exist on the planet and they are not ready to disappear just yet. Every day, totally new gadgets are designed and manufactured some are even very expensive. But do we need them? Are they the best use of our resources?
Is low price equal to poor quality? Certainly not look at car brands today. Lets take Renault as example. They have a more economical product line called Dacia and it has one of the highest customer reliability ratings on the market (as perceived by customers)!
If a company finds a defect in one of their products and makes a product recall, customer reliability and therefore production will decrease because trust in the products quality will be lost. It does not come more simple than that. People who tell you anything different do not see customers are their primary reason for existence. And If you don’t believe that, try doing without customers for a while!
So if this is the case, why can it be so difficult to improve quality in an organisation? For a very simple reason. Many people still assume that Better Quality equals More Cost. In their mind, more control (inspections and checks/lab tests) are needed, more people are involved, more defective goods will be found and destroyed. All of this costs more money, increases the manufacturing price of the product, and so on.
Here is how I view it and I have experienced it. You CANNOT inspect quality into products. Instead you design quality into products. When you have defective products, start verifying every process step from design to delivery to the customer. Do not assume that all was done properly but verify, always! You are likely to find some interesting things that can be improved. Once you have the root cause(s), communicate corrective and preventive actions to all parts of the company and supply chain. All can learn and benefit from the mistakes made in the past. It helps guard against them in the future. Equally important is communicating on the success of a quality-improved product. Based on good examples, build your future with success.
However, this is not the only thing crucial to success in quality. Employee Training is so often undervalued and under supported. Training makes employees more skilled and knowledgeable which often leads to greater involvement in quality processes. The involvement of all employees is key! Without total employee involvement, any Quality department in any organization will Fail. Employees must be trained in the “whys” and “how tos” of quality and what it means to the employees, the organization and most importantly for the Customers. For some this is revolution; for others this is evolution.
And for those readers who dont agree with my approach, I would suggest do not assume, just verify. Read the works of quality experts like Dr. Joseph M. Juran, Dr. W. Edwards Deming and Philip B. Crosby, Professor Yoji Akao, Walter A. Shewhart, David Garvin, or implement the Baldrige Criteria, or Honshin Kanri (Deming cycle), or QFD, or the Pareto principle, Kaizen (QC), the EFQM, and many more.
Remember Quality is not a necessity. if you do not want to survive in the long term.
Testing the Concept (New Product Development) Part 4
This is the third in the series of articles helping you through the New Product Development process.
We will be focusing on this step:
Phase Objectives
Concept testing is carried out after the idea screening. The objective of this phase is to determine the following:
- Gain an understanding of what potential buyers and customers think of the product concept
- Determine if the market is ‘ready’ for the new product (i.e. can the product sell?)
- Understand what changes are required from the initial feedback given by those customers that have reviewed the concepts
Concept testing is included within the process so that any organization can predict the success of a new product idea before that idea progresses through too many more stages which inevitably will begin to increase the required financial investment.
Another major part of this phase is to ensure you have completed all the relevant patent searches, carried out all the design due diligence, and covered all the other legalities involved with new product development.
Methods for getting feedback from customers
There are a number of different methods used to present product concepts to customers in order to obtain feedback; we cover just a few below.
Focus Groups
The Market Research Association defines a focus group as ‘the meeting of a small group of individuals who are guided through a discussion by a trained moderator (or consultant). The goal of the focus group is to get beyond superficial answers and uncover insights on consumer attitudes and behavior’.
From your business point of view, the focus group could be made up of a number of long standing and trustworthy customers, a number of staff at different levels within your organization, other like-minded business professionals, and potential investors.
All focus groups should have a moderator to manage and guide the group through the process of reviewing the concepts and Q&A sessions.
At the end of the focus group session you should have a better understanding of what the general feedback is, and on what areas you need to work before moving forward with development.
Survey and Questionnaires
You need to approach a significant sample of people who match the profile of your target audience when conducting surveys and sending out questionnaires. Unless people care about the product or service, youll find that response rates are generally low.
Market research questionnaires are a well-known way of generating market information. Questionnaires are typically used to produce numbers. For example, how many potential customers are there in the local area, whether they would find such a product or service useful, and the sort of price they would be willing to pay for it. The key is to ask the right people the right questions, and to ask enough people to get meaningful results. (Source: marketingdonut ).
Feedback and what to do with it
From all the marketing research and concept idea testing, you should be able to determine the following attributes:
- What product features must be incorporated into the design
- What the benefits of each feature are
- How the customer will react to the product when it reaches the market
- Pricing points (this may differ depending upon feature list)
- Areas of the design that need to be changed, modified or eliminated
With a more solid product specification you should be able to move forward into the next development phase with confidence.
Patents and Due Diligence
If you are asking yourself “do I need to worry about patents?”, the short answer is YES. It is important that you do not infringe any intellectual property rights (IP) that belongs to somebody else. The simplest way to find this out is to carry out patent searches to check whether your design or product is OK. This also allows you to consider the information before thinking of filling for your own patent and owning your own IP.
A quick method of searching for patents is www.google.com/patents .
If you are thinking of applying for your own patent, E. Blum & Co suggests the following:
1. What can be patented?
For an idea to be patentable, it has to fulfil various criteria, in particular:
- An invention has to be new. In order to be new, it has to differ from everything known to the public. Note: It is often the inventor herself/himself who destroys the novelty of his idea by disclosing his ideas to a third party without secrecy agreement.
- An invention must not be obvious in regard to the state of the art. Obviousness has to be judged from the point of view of an expert skilled in the relevant technical field. It must be determined what problem the putative invention solves in comparison to known solutions in the field. If the state of the art encourages or leads the expert to choose a certain solution to this problem, this solution is considered to be obvious if not, the solution is considered to be inventive.
- An invention must have technical character. A method for doing business is, in many countries, not patentable. However, as soon as for example a technical problem is solved or technical considerations are required, it may be patented.
Naturally, we must state that we are not providing any legal advice here. We suggest you discuss these matters with your lawyer.
2. Due Diligence
From a new product development point of view, carrying out due diligence is all about making sure all the legal aspects have been covered so that when your product gets to market there are no nasty surprises. Make sure everything is documented and recorded for future reference.
End of Phase 3
At the end of each phase there should be a review meeting that goes over all the key elements and information from that phase. We already touched on this in the last article.
There is a procedure to follow for each of the phase reviews that results in a decision for the project (does it STOP, GO, or REVISIT) before proceeding onto the next phase. This review meeting is commonly referred to as a Stage Gate Review with the stop/go being the gate for the next phase.