A primer on waterjet accessories
Post on: 6 Апрель, 2015 No Comment
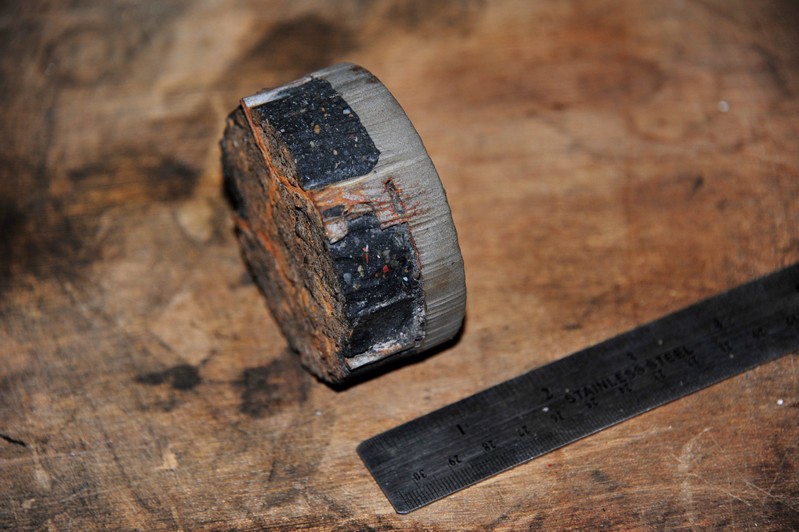
New waterjet users should be aware of recent technological advancements
January 17, 2011
For fabricators and metalworkers considering their first purchase of a waterjet, return on investment will be heavily influenced by features, options, and accessories that provide a match to their unique needs.Investigating and evaluating the latest alternatives will go a long way in boosting profitability.
Figure 1: At the International Manufacturing Technology Show 2010 in Chicago last September, attendees showed interest in what bevel cutting on a waterjet might mean for some of the complex beveled parts they fabricate.
Over the past several years, significant changes have taken place in the realm of waterjets. Machines have become more accurate; more features have broadened their applicability; and most important for many manufacturers, the technologys cost of entry has decreased.
An increasing number of fabrication and metalworking shops have purchased or are considering their first abrasive waterjet cutting center. Getting the most out of this investment requires taking the time to learn about and evaluate some of the options and accessories now available to shops.
Controlling the Cut
Of all the waterjet advancements in recent years, most of them have enhanced the machines cutting capabilities. For example, the ability to cut bevels is getting the attention of complex-part fabricators. This bevel cut is achieved through the combination of a tilting nozzle and computer software to control its movement. The capability allows for the cutting of components with complex geometries (see Figure 1 ) and also provides beveled edges to prepare parts for welding operations, achieving both cost and time savings.
Terrain-following features (see Figure 2 ) offer another benefit. These accessories track material surface heights and compensate for variation to maintain the proper standoff throughout the cutting process. This proves especially valuable to shops working with large sheets of material that have uneven surfaces or become warped during cutting due to stress relief. The use of a terrain-following accessory greatly reduces setup times, as it eliminates the need to locate and program around material high points.
ADVERTISEMENT
While still in its introductory stages, the ability to etch 3-D shapes (see Figure 3 ) further increases the advantages waterjet technology offers. At present this capability is limited to producing shapes and features with low accuracy requirements, such as in artistic applications or identification markings. Because this technology is driven by software, though, todays new waterjet adopters will be able to benefit as etching becomes more refined.
Rotary axis accessories (see Figure 4 ) offer another perspective on how waterjet is evolving to apply to 3-D components. Shops incorporating this relatively new capability typically use it to cut pipes. Coupled with bevel-producing cutting heads, a rotary axis allows cutting of pipes that are prepped for welding operations.
While not as new as some other features, taper-removing tilting heads continue to increase the value of waterjet machines. The cutting stream produces a tapered kerf, the degree of which varies with cutting speed. Traditionally, programmers would move slowly in critical areas, reducing the cost benefits of waterjet technology. Taper-removing nozzles adjust for this, changing the angle of the cutting stream to transfer taper to the scrap material and leave a square edge on the part.
Boosting Productivity
Several newer options located apart from the waterjet head allow fabricators to increase the productivity of their abrasive waterjet machines. Many larger models now can accommodate a second, independently controlled Y-bridge. Machines incorporating this layout can program the two bridges to produce separate, smaller parts or to work together on larger components. With either scenario, substantial productivity gains may be realized.
Waterjet operators also can add a second pump to their machines. The use of two pumps does several things:
- It increases the maximum volume of water pumped through a nozzle, boosting cutting speeds dramatically.
- A two-pump system offers an obvious advantage to those who have integrated a second Y-bridge, as otherwise each nozzle would have reduced flow.
- 3. Last, adding a second pump minimizes machine downtime, as one pump can be used to keep the machine running while the other undergoes routine maintenance.
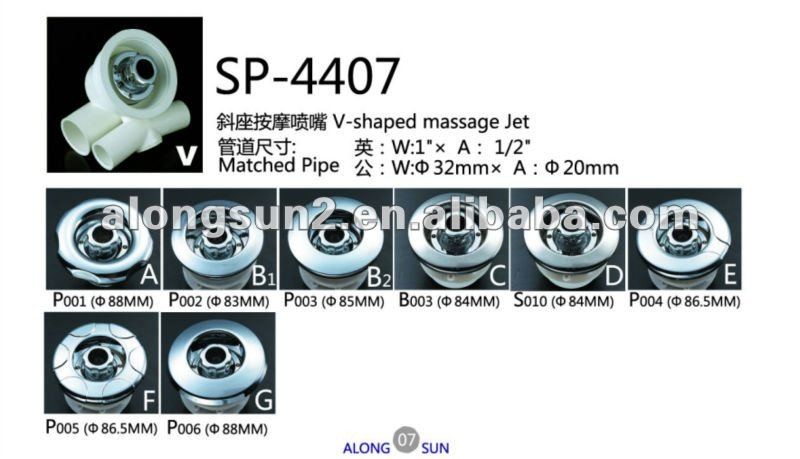
Handling Garnet
The degree to which abrasive handling should be automated depends heavily on how much a shop operates its abrasive waterjet center. Light users can manually load garnet, the sandlike material that performs the actual cutting in abrasive waterjet applications. For shops that operate a machine more frequently, accessories can prove useful.
Figure 2: Terrain-following accessories ensure a consistent waterjet cut on material with inconsistent surface heights.
A garnet feeder delivers the material to the machine via a pneumatic conveyor system. The operator loads a large amount of garnet into a pressure pot, and then air pressure of 20 to 50 PSI propels it through a hose to a smaller chamber located close to the nozzle. Usually this chamber accommodates enough garnet to allow the pressure pot to be reloaded without stopping the machine, allowing continuous operation.
Garnet removal is an important aspect of machine operation. A pump transfers water from the machine to a large hopper, where garnet settles to the bottom. The pump then returns the water to the machines catcher tank. The cutting action of the machine typically generates enough motion within the tanks contents to keep the garnet circulating until the water can be removed. In some environments, though, a second pump must be added to power low-pressure jets within the tank to keep the garnet fluidized. Determining the necessity of such an accessory requires evaluation of the specific applications being performed.
Last, a shop must consider how its environment will affect the garnet. With high levels of humidity, moisture can bond the garnet together and impede its flow. At the other end of the spectrum, extremely dry conditions can create a similar problem when static electrical discharge bonds the garnet. In either of these cases, a shop should integrate an abrasive agitator that uses vibration to keep the garnet in an ideal state.
Taking the Plunge
Since its inception, abrasive waterjet has provided clear productivity gains. In recent years technological breakthroughs have expanded the technologys applicability, allowing a far larger and more diverse array of companies to utilize its capabilities.
For fabricators and metalworkers considering their first purchase of a waterjet, return on investment will be influenced heavily by the selection of features, options, and accessories that provide a match to their unique needs. Investigating and evaluating the latest alternatives will go a long way in boosting profitability.