25Seven The True Cost of an Eccentric Bottom Bracket Shell
Post on: 21 Апрель, 2015 No Comment
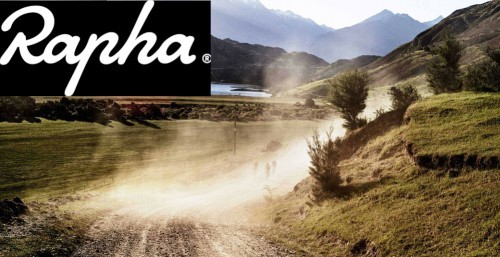
December 26, 2008
The True Cost of an Eccentric Bottom Bracket Shell
The Eccentricities of Eccentric BBs
Recently, someone gave Seven Cycles a hard time for charging extra for our eccentric bottom bracket—BB—shell option.
To help normal people understand this gibberish, the bottom bracket shell is where the crank set and pedals fit onto the frame.   Seven offers three BB shell options:
- Standard threaded shell ; it’s been around for many years
- Eccentric shell “EBB”, for special purpose bikes
- BB30 shell ; this week’s industry “standard”
As our friendly skeptic put it, when referring to the optional BB shell, “ it’s just a piece of pipe, so how can you charge extra?”   How much simpler could this option be, right?   Heck, we should probably have a price reduction since it’s so much “easier” than our standard threaded shell.   That’s for sure.
It’s a reasonable question.   When asked in a reasonable way.   I can definitely see why it may seem a lot simpler than our standard threaded BB shell.   After all, it is true that our standard BB shell is a complicated and expensive part:
- The shell is threaded on both ends—with one thread in reverse.   And it’s a very tight tolerance thread.
- We face both ends of the shell to within 0.001” tolerance .
- We ensure that the shell’s axis is in alignment to the frame to within 0.001” tolerance.
- The centerline of the shell to the frame is within 0.002” tolerance.
- We even counter bore the shell between the threads to remove additional weight.
- The shell has a few interrupted cuts—because of breather holes required for welding—that wreak havoc on cutters.
Because of the requirements for all these tight tolerances, we actually CNC—computer numerically control—machine the shell after it’s been welded into the frame.
Well, Seven’s standard threaded shell sure seems like a lot of work when compared to an eccentric shell that’s “just a simple pipe”, right?   Nope.   Heres why the EBB is not easier, and why it actually costs just a bit more than our standard threaded BB shell.
Looks Can Be Deceiving
We have three basic elements that impact the cost of the EBB option:   fixturing, labor, and materials.   As with most tight tolerance manufacturing that includes high-end steels and titanium alloys, these three elements are costly.   Of course, cost is relative—relative to our standard threaded BB shell.
Cost of Material
Seven designed our standard BB shell system from scratch.   This includes the titanium starter stock material.   We had tubing mandrels made by the titanium mill; we actually own the mandrels.   This is expensive.   We did this, in spite of the cost, because the shell material that was available did not suite our ideal design criteria precisely.   We even employ a slightly different material specification for our BB shells than our other titanium tubing; we tailor the specs to the task at hand.  
Because of Seven’s special requirements for sizing and specification, we have to order directly from a titanium mill at a minimum order of 300 feet at a time—about 1,000 bikes worth.   No Toyota Production System thinking or single-piece-flow here.
Conversely, for the eccentric BB shell, because the volume is so low, there is no reasonable opportunity to design the ideal tube from scratch.   The market does not exist for investing in the tooling.   Therefore, we work with preexisting material.   The two basic options are solid bar stock or oversized “pipe”.   Both of these starting points require significant modification and preparation before we can even begin building a frame.  
The Cost of Process and Labor
The bottom bracket shell is the starting point—the foundation—for every frame.   So, when we change that anchoring point, many steps in the process change, and some of the frame elements also require modification.
Here are some examples of the process differences between Seven’s standard BB and our eccentric BB:
.  The coping of tubes to fit to the special shell size:   The diameter is different, and of course, it’s an odd size; it’s 2.25”, and not so convenient.   It’s large enough that we had to modify a lot of our tooling for cutters to fit.
  Frame jig modification.   Not only is the shell diameter different, the width is also different.   Both of these factors mean specialized fixturing for tacking the frame and ensuring frame alignment.
  Welding :
          .   Requires a special oxygen purge adapter for the oversized shell.  
          .   The shell is both a lot larger diameter and thinner than our threaded shell.    This requires a lighter welding touch because the thinner shell could distort a lot more than the thicker threaded shell; all the while ensuring that enough heat is present for complete weld bead penetration.
.   CNC machining.   Even though it’s “just a pipe”, we still choose to run it through our CNC machine to ensure we meet all the important tolerances:
          .  Inside diameter is precisely round and accurate.   If the parts don’t fit exactly correct, the eccentric insert can slide around.   In additional, we have designed the system to be thicker than needed before CNC machining because we know there will be some distortion due to the welding process.
          .  We hold all the same tolerances we have for our threaded BB shells:   centerline, shell axis alignment, and facing standards.
 Final frame alignment check:   The oversized shell requires a more complex multistage alignment system, in large part because the eccentric element is a separate part installed after the frame is complete.
  Final assembly.   this part—the Bushnell eccentric—is installed at Seven.   Conversely, on a standard threaded shell, there is no part to install at Seven.
All this adds time to each frame—significant time.   It definitely takes more time to build an EBB frame than a threaded shell frame.   In part because the starter stock requires a lot of preparation work, in part because of all the tooling changes required, and in part because the EBB is a lot more sophisticated than a simple “pipe”.
Cost of Tooling
Nearly every one of the steps mentioned above require special dedicated—or at least modified—fixturing or tooling for machining, tacking, welding, purge system, and CNC machining.   Seven has invested thousands of dollars in special EBB tooling to ensure the end product meets the customer’s expectations.  
Cost of the Insert
The final step—and cost incurment—in Seven’s eccentric BB option, is the inclusion of a Bushnell eccentric insert with each shell.   We feel it’s critical to include because you can’t build up the bike without it.   And most retailers would not be too excited about sourcing that part. 
I don’t recall the suggested retail price on just the aluminum parts from Bushnell, but based on the price we pay for the part, I would expect the parts, by themselves, to retail for at least $200—it’s a very pretty, and well designed, part.   So, a customer could figure out that the majority of Seven’s upcharge for the EBB option is actually due to the aluminum insert—not the “pipe” itself.
I have to agree; it does seem like a lot of work for a specialty option that not many riders choose.   Maybe we should stop
So, why do we even bother offering an EBB if it’s so much work?   Well, it’s what we do; we build custom frames and bikes.   The EBB is one important option in our customization arsenal.   In fact, we first offered the EBB back in 1998 due to a need based on our tandem market.   We are committed to tandems and the type of tandems we wanted to offer required an EBB system.   Therefore, the EBB option is here to stay at Seven.   It works really well for the right type of specialty bike.
The Cost of Value
Not bad for all that work.   Even though it is “just a pipe.”   Looks can be deceiving.   Simple does not always equal less expensive.